Redis的哨兵保驾护航:安全可靠的数据管理
在使用Redis时,出现宕机、网络故障等异常情况是难免的,这时候我们需要保证数据的安全性和可靠性。Redis的哨兵机制为我们提供了一个保障,即使出现异常情况,我们依旧可以恢复数据的完整性。下面将介绍Redis哨兵机制的基本原理与实现。
一、Redis哨兵机制的原理
Redis哨兵机制的核心是哨兵进程(sentinel),它能够监控被监管的Redis实例的状态,并在主Redis发生故障时向从Redis节点切换,从而保证数据的可靠性。当哨兵进程检测到主节点失效后,它会选择一个从节点作为新的主节点,并将其他从节点和客户端重定向到新的主节点。当主节点重新上线时,哨兵还能自动将它重新设置为主节点。
二、Redis哨兵机制的实现
1.启动哨兵进程
使用Redis默认安装的redis-sentinel命令可以启动哨兵进程,命令格式为:
redis-sentinel /path/to/sentinel.conf
其中,sentinel.conf是Redis哨兵配置文件的路径。在此配置文件中,包含了被监控的Redis实例的相关信息,如IP地址、端口号等。
2.监控Redis实例的状态
哨兵进程会周期性地向被监管的Redis实例发送ping命令,以检测它们的状态。如果一个Redis实例在一定时间内连续多次无响应,哨兵就会判定该实例已经失效。此时,它会发布一个主观下线通知,这个通知会被其他哨兵和客户端接收。当足够多的哨兵和客户端观察到同一个Redis实例失效时,就会发布一个客观下线通知。哨兵进程会在客观下线通知收到后,向其他哨兵进程发送请求来确认这个Redis实例是否真的宕机了。
3.从节点选举新的主节点
如果一个主节点失效了,哨兵进程将会从当前的从节点中选出一个做为新的主节点,并向其他从节点和客户端返回一个切换命令,将它们重定向到新的主节点。选举的依据主要包括优先级、最近一次同步的复制偏移量、复制积压缓冲区大小等。在选举完成后,哨兵进程会将选举结果写入Redis的系统信息中,以备其他哨兵和客户端使用。
4.故障恢复
一旦失效的Redis主节点重新上线,哨兵进程会自动将它恢复为原来的主节点。为了防止因网络延时等原因引起误判,哨兵会设置一个默认的故障恢复时间,这个时间之前的任何意外重启都不会被认为是节点恢复。
总结
Redis哨兵机制是Redis的高可用性方案之一,可以保障数据的安全和可靠性。哨兵进程的启动、监控Redis实例状态、从节点选举新的主节点、故障恢复等步骤,在保证数据一致性的同时,还能提高了Redis系统的可用性和可靠性。为了更好地保障数据安全,同时我们也应该在Redis数据备份和权限管理上下功夫。
香港服务器首选树叶云,2H2G首月10元开通。树叶云(shuyeidc.com)提供简单好用,价格厚道的香港/美国云 服务器 和独立服务器。IDC+ISP+ICP资质。ARIN和APNIC会员。成熟技术团队15年行业经验。
2003年产原装奥迪A4轿车 有时发动机会熄火,啥原因? 1.8T涡轮增压发动机,01J型无级变速器。 每次重新起动发动机后第一次挂R挡接合非常平顺,第二次再挂便开始冲击,同时假如反复操纵冲击力就会越来越大,有时会使发动机立即熄火。
通过仔细试验,我们总结出一个规律:
①每次重新起动发动机后第一次挂R挡接合非常平顺,第二次再挂便开始冲击,同时假如反复操纵冲击力就会越来越大,有时会使发动机立即熄火。
②让变速器在前进挡上运行一会儿再挂R挡,第一次还是非常柔和,接下来再操纵又开始冲击。
③起动发动机第一次换挡杆由P/N进R挡时接合平顺,此时假如将换挡杆拉进N位或P位,停留1min后再次挂进R挡,则冲击力消失。
根据实际故障现象,我们应该把故障定义为“R挡压力控终光目”。 由于假如R挡压力过高或调节不正常都会导致R挡接合粗暴。 对于奥迪01J无级变速器,发动机与变速器之间不像自动变速器那样通过液力变矩器来传递动力,而是通过两组用油元件即前进挡离合器和倒挡制动器,通过机械方式来传递发动机动力,因此车辆在静止时踩制动踏板进动力挡(R、D)的控制是:
①离合器或制动器压力低。
②发动机输出扭矩小(即链条与链轮之间的夹紧力小)。
因此无论是前进挡离合器压力还是倒挡制动器压力在车辆静止接合、行驶中及在发动机各种工况下的输出扭矩下都必须保持合适的工作压力。 假如倒挡压力不正常,既涉及到控制单元的指令,又涉及到液压的控制,同时还涉及到倒挡机械执行元件本身。 在奥迪01J无级变速器上,前进挡离合器和倒挡制动器的压力电子调节控制,主要是控制单元通过接收“发动机转速”(通过CAN与发动机控制单元通讯)、“变速器输进转速”(主动传动链轮转速由G182传感器提供)、“加速踏板位置”(通过CAN与发动机控制单元通讯得知油门踏板所处的位置)、“发动机输出扭矩”(通过监测链轮与传动链条之间接触压力计算出由压力传感器G194提供)、“制动力”(通过CAN由ABS控制单元提供)及“变速器油温”(通过G93油温度传感器计算出)等参数逻辑分析后,计算出前进挡离合器或倒挡制动器的额定压力,并且由此确定出压力调节电磁阀N215的控制电流。 这样不同的控制电流便产生不同的离合器或制动器的控制压力,因此离合器或制动器传递发动机的扭矩也相应地随控制电流的变化而变化。 压力传感器G193监测液压控制系统中离合器或制动器的实际压力,实际离合器压力与变速器控制单元计算出的额定压力不断进行比较(实际压力与额定压力通过模糊理论被持续监控),若两者差值超过一定范围,便会进行修正,这样便形成前进挡离合器和倒挡制动器压力控制原理图。
离合器或制动器压力与发动机扭矩成正比,与系统压力无关。 通过离合器压力控制油路图,液压控制阀体中的输导压力阀(VSTV)始终为压力调节电磁阀N215提供一个500kPa的常压,根据变速器控制单元J217计算的控制电流值,压力调节电磁阀N215就会调节出一个控制压力,该压力的大小就会决定离合器控制阀(KSV)的位置。 离合器控制阀KSV根据N215的触发信号(电流的大小)产生离合器或制动器的控制压力,高控制压力产生高离合器压力,离合器压力通过安全阀SIV传递得手动阀HS,手动阀的位置改变就会将扭矩传递到前进挡离合器(D位置)或倒挡制动器(R位置),当换挡杆位于P、N位置时,手动换挡阀切断供油,前进挡离合器和倒挡制动器的油路都与油底壳相通,离合器的压力也会随车速的变化而变化。 G193压力传感器是监测前进挡离合器和倒挡制动器真实压力的,并把真实信息再反馈给控制单元J217,并再次修正N215电磁阀的工作电流,以便实现合适的离合器或制动器压力,同时输出扭矩的变化由压力传感器G194实时监控。
通过对奥迪01J无级变速器离合器及制动器压力控制的了解,同时结合该车的实际故障现象(R挡冲击),故障诊断思路比较明确:各重要输进信息、控制单元J217对N215电磁阀的指令、N215电磁阀本身性能、阀体中离合器控制阀的磨损程度及倒挡制动器本身工作性能等。 因此,我们首先对该车的发动机电子控制系统以及变速器的电子控制系统进行检测。 检测发动机电控系统时,未发现各数据异常。 但在变速器电子控制系统的故障存储器中却发现了号故障码,该故障代码含义为变速器输出转速传感器2(G196)不可靠信息。 由于是偶发故障,因此清除故障存储之后再没有重新出现暂且不作考虑。 接下来我们必须具体了解变速器在执行R挡时的动态数据,以便分析故障部位。
利用故障诊断仪进进变速器02-01读出该变速器控制单元数据,控制单元:01JCP组件编码:V3001J1。 815VTRdW2011,控制单元编码服务站代码:WSC。 针对该车倒挡故障重点观察数据流第11组数据和第18组数据,主要对比正常状态下和非正常状态下数据值的变化。 进进02-08-011组,在换挡杆置于R位置制动未行驶时,第1项数据是0。 295A(N215工作电流),第2项数据是“自适应运行中”(制动器适应状态),第3项是83℃(变速器温度),第4项是15N·m(输出扭矩);进进02-08-018组数据,第1项数值是430kPa~520kPa(制动器压力值G193提供),第2项数值是15~18N·m(输出扭矩),第3项数值是180kPa(链轮与链条之间接触压力G194提供),第4项数值是0。 230~0。 325A(N215电磁阀工作电流)。
通过对两组数据的分析,011里第2项数据制动器适应状态在“自适应运行中”是不正常的,同时在018组数据里制动器压力似乎有些偏高,且N215电磁阀工作电流相对也很不稳定。 无论怎样,我们首先都必须要匹配倒挡制动器的适应压力。 通过反复倒车、制动02-08-011组的第2项数值由原来的“自适应运行中”变为“自适应成功”,但故障现象依然存在。 反复观察各动态数据,我们以为控制单元指令几乎都很正常,因此在操纵简单的情况下我们决定更换液压控制阀体试一下。
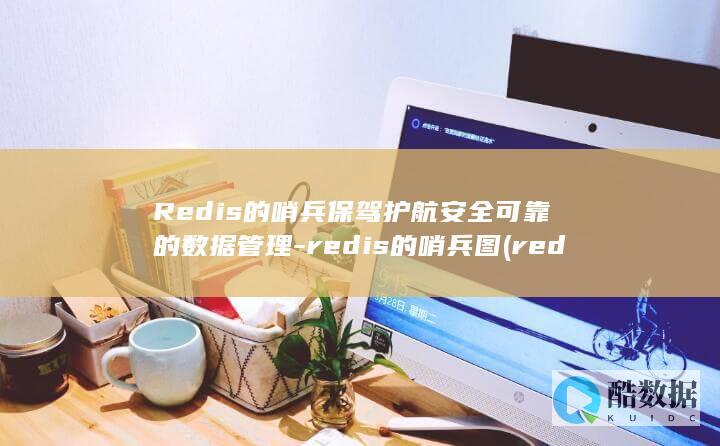
由于不敢100%判定更换阀体即可解决题目,先找了1个旧的阀体装车试验,结果故障没有丝毫改变。 但通过对数据进行分析,控制单元的可能性还是比较小,由于我们反复捕捉R挡冲击时的动态数据发现,当R挡冲击非常严重时,在018组里第1项数占有时达到1170kPa~1200kPa,但N215电磁阀工作电流变化并不大,它在0。 225~0。 305A之间变化,而N215在0。 305A的电流驱动下不可能实现1200kPa的压力;当R挡冲击不严重时,在018组里第1项数据在520kPa左釉冬同时N215电磁阀工作电流也在0。 235A左釉冬此时我们还记录了P挡位和D挡位的018组数据:P挡位第1项为380kPa,第2项为15。 0N·m,第3项为270kPa,第4项为0。 295A。 D位第1项为230kPa,第2项为18。 0N·m,第3项为270kPa,第4项为0。 295A。 此时大家觉得题目应该还是在液压控制方面,这样又继续更换两块阀体,但题目仍然没有得到改善。 在这种情况下,我们以为不可能所有更换过的阀体都有同样的题目,因此又费尽周折找到一块型号为01JCP的控制单元,结果装车后故障依旧。 此时有人说既然阀体和控制单元都换过了,应该是控制单元软件匹配升级的题目,为此我们又到奥迪4S店利用VAS5051对电子控制单元进行软件升级处理,但没有任何效果。
静下心来仔细对故障现象再重新进行具体分析,为什么让变速器在前进挡上运行一会再挂R挡,第1次还是非常柔和的,同时起动发动机第1次换挡杆由P/N进R挡时接合平顺,此时假如将换挡杆拉进N位或P位,停留1min后再次挂进R挡,冲击力也会消失。 这不就是R挡压力油的回油速度题目吗?R-N-R-N或R-P的切换完全就是靠手动阀切换的,因此题目一定来源于阀体和R挡制动器本身。 既然阀体更换多个,因此早已排除,剩下就是R挡制动器。 万般无奈之下,从车上将变速器抬下,更换前进挡离合器和倒挡制动器总成(带输进轴、输进齿轮位43齿),此时故障彻底排除。 之后,我们又把竣工后的各挡正常数据采集下来。 02-08-018组P挡位:①3~4kPa。 ②15.0N·m。 ③200kPa。 ④0.290→0.295→0.300A。 R挡位:①3→1→4→5→6→7kPa。 ②15→6→0→3→5→9→12→15→18N·m。 ③200kPa。 ④0.290→0.245→0.260→0.270→0.285→0.295A。 D挡位:①3→2→3→400kPa。 ②15→24→18N·m。 ③300kPa。 ④0.295→0.340→0.300→0.305A。 02→08→011组R挡位:①0.295A。 ②自适应成功。 ③83℃。 ④15→0→3→9→12→18N·m。
总结:对于01J无级变速器故障的分析必须以数据为根据,由简到难逐一将电、液及机械分开,终极找到故障点。 找到故障点后,无非就是更换部件的题目,但必须要熟练把握并了解01JCVT相关知识。 就此故障而言,我们不可能接车后就马上更换前进挡离合器和倒挡制动器总成,由于那是没有道理的,但更换控制单元似乎是一个额外的小插曲。 推荐你一款叫“汽车维修大师”的手机app,你可以下载一个,平时我都是在这上面了解关于车辆的信息。
船舶制造的分类
车间的划分常根据船厂的生产规模、性质、习惯而有所不同。 过去很多造船厂除进行钢材加工、船体装配、焊接和设备系统安装外,还具有一定的铸、锻和机械加工能力,在制造船体的同时还制造主机、辅机、锅炉等设备。 20世纪50年代以来,随着造船及其配套工业的发展,造船厂已向总装方向发展,即以建造船体为主,大量的机电设备和舾装件则由专业或非专业的协作厂配套提供,船厂只进行安装,以提高造船质量和效率。 造船工序造船的主要工艺流程可用下面的框图表示。 钢材预处理在号料前对钢材进行的矫正、除锈和涂底漆工作。 船用钢材常因轧制时压延不均,轧制后冷却收缩不匀或运输、储存过程中其他因素的影响而存在各种变形。 为此,板材和型材从钢料堆场取出后,先分别用多辊钢板矫平机和型钢矫直机矫正,以保证号料、边缘和成型加工的正常进行。 矫正后的钢材一般先经抛光除锈,最后喷涂底漆和烘干。 这样处理完毕后的钢材即可送去号料。 这些工序常组成预处理自动流水线,利用传送滚道与钢料堆场的钢料吊运、号料、边缘加工等后续工序的运输线相衔接,以实现船体零件备料和加工的综合机械化和自动化。 放样和号料船体外形通常是光顺的空间曲面。 由设计部门提供的用三向投影线表示的船体外形图,称为型线图,一般按1:50或1:100的比例绘制。 由于缩尺比大,型线的三向光顺性存在一定的误差,故不能按型线图直接进行船体施工,而需要在造船厂的放样台进行1:1的实尺放样或者是1:5、1:10的比例放样,以光顺型线,取得正确的型值和施工中所需的每个零件的实际形状尺寸与位置,为后续工序提供必要的施工信息。 船体放样是船体建造的基础性工序。 号料是将放样后所得的船体零件的实际形状和尺寸,利用样板、样料或草图划在板材或型材上,并注以加工和装配用标记。 最早的放样和号料方法是实尺放样、手工号料。 20世纪40年代初出现比例放样和投影号料,即按1:5或1:10的比例进行放样制成投影底图,用相应的低倍投影装置放大至实际尺寸;或将投影底图缩小到1/5~1/10摄制成投影底片,再用高倍投影装置放大50~100倍成零件实形,然后在钢材上划线。 比例放样还可提供仿形图,供光电跟踪切割机直接切割钢板用,从而省略号料工序。 投影号料虽在手工号料的基础上有了很大改进,但仍然未能摆脱手工操作。 60年代初开始应用电印号料,即利用静电照相原理,先在钢板表面喷涂光敏导电粉末,进行正片投影曝光,经显影和定影后在钢板上显出零件图形。 适用于大尺寸钢板的大型电印号料装置采用同步连续曝光投影方式,即底图和钢板同步移动,在运动过程中连续投影曝光。 适用于小尺寸钢板的小型电印号料装置,则在钢板上一次投影出全部图形。 这种号料方法已得到较广泛的应用。 随着电子计算机在造船中的应用,又出现数学放样方法。 即用数学方程式表示船体型线或船体表面,以设计型值表和必需的边界条件数值作为原始数据,利用计算机进行反复校验和计算,实现型线修改和光顺,以获得精确光顺和对应投影点完全一致的船体型线。 船体的每条型线都由一个特点的数学样条曲线方程表示,并可通过数控绘图机(见绘图用具)绘出图形。 数学放样可取消传统的实尺放样工作,还可为切割和成形加工等后续工序提供控制信息,对船体建造过程的自动化具有关键的作用,是造船工艺的一项重要发展。 船体零件加工包括边缘加工和成形加工。 边缘加工就是按照号料后在钢材上划出的船体零件实际形状,利用剪床或氧乙炔气割、等离子切割进行剪割。 部分零件的边缘还需要用气割机或刨边机进行焊缝坡口的加工。 气割设备中的光电跟踪气割机能自动跟踪比例图上的线条,通过同步伺服系统在钢板上进行切割,它可与手工号料、投影号料配合使用。 采用数控气割机不但切割精度高,而且根据数学放样资料直接进行切割,可省略号料工序,实现放样、切割过程自动化。 对于具有曲度、折角或折边等空间形状的船体板材,在钢板剪割后还需要成形加工,主要是应用辊式弯板机和滚压机进行冷弯;或采用水火成形的加工方法,即在板材上按预定的加热线用氧-乙炔烘炬进行局部加热,并用水跟踪冷却,使板材产生局部变形,弯成所要求的曲面形状。 对于用作肋骨等的型材,则多应用肋骨冷弯机弯制成形。 随着数字控制技术的发展,已使用数字控制肋骨冷弯机,并进而研制数字控制弯板机。 船体零件加工已从机械化向自动化进展。 船体装配和焊接将船体结构的零部件组装成整个船体的过程。 普遍采用分段建造方式,分为部件装配焊接、分段装配焊接和船台装配焊接3个阶段进行。 ①部件装配焊接:又称小合拢。 将加工后的钢板或型钢组合成板列、T 型材、肋骨框架或船首尾柱等部件的过程,均在车间内装焊平台上进行。 ②分(总)段装配焊接:又称中合拢。 将零部件组合成平面分段、曲面分段或立体分段,如舱壁、船底、舷侧和上层建筑等分段;或组合成在船长方向横截主船体而成的环形立体分段,称为总段,如船首总段、船尾总段等。 分段的装配和焊接均在装焊平台或胎架上进行。 分段的划分主要取决于船体结构的特点和船厂的起重运输条件。 随着船舶的大型化和起重机能力的增大,分段和总段也日益增大,其重量可达800吨以上。 ③船台(坞)装配焊接:即船体总装,又称大合拢。 将船体零部件、分段、总段在船台(或船坞)上最后装焊成船体。 排水量10万吨以上的大型船舶,为保证下水安全,多在造船坞内总装。 常用的总装方法有:以总段为总装单元,自船中向船首、船尾吊装的称总段建造法,一般适用于建造中小型船舶;先吊装船中偏尾处的一个底部分段,以此作为建造基准向船首、船尾和上层吊装相邻分段,其吊装范围呈宝塔状的称塔式建造法;设有2~3个建造基准,分别以塔式建造法建造,最后连接成船体的称岛式建造法;在船台(或船坞)的末端建造第一艘船舶时,在船台的前端同时建造第二艘船舶的尾部,待第一艘船下水后,将第二艘船的尾部移至船台末端,继续吊装其他分段,其至总装成整个船体,同时又在船台前端建造第三艘船舶的尾部,依此类推,这种方法称为串联建造法;将船体划分为首、尾两段,分别在船台上建成后下水,再在水上进行大合拢的称两段建造法。 各种总装方法的选择根据船体结构特点和船厂的具体条件而定。 船体装配和焊接的工作量,占船体建造总工作量的75%以上,其中焊接又占一半以上。 故焊接是造船的关键性工作,它不但直接关系船舶的建造质量,而且关系造船效率。 自20世纪50年代起,焊接方法从全手工焊接发展为埋弧自动焊(见埋弧焊)、半自动焊、电渣焊、气体保护电弧焊。 自60年代中期起,又有单面焊双面成形、重力焊、自动角焊以及垂直焊和横向自动焊等新技术。 焊接设备和焊接材料也有相应发展。 由于船体结构比较复杂,在难以施行自动焊和半自动焊的位置仍需要采用手工焊。 结合焊接技术的发展,自60年代起,在船体部件和分段装配中开始分别采用 T型材装焊流水线和平面分段装焊流水线。 T 型材是构成平面分段骨架的基本构件。 平面分段在船体结构中占有相当的比重,例如在大型散装货船和油船上,平面分段可占船体总重的50%以上。 平面分段装焊流水线包括各种专用装配焊接设备,它利用输送装置连续进行进料、拼板焊接以及装焊骨架等作业,能显著地提高分段装配的机械化程度,成为现代造船厂技术改造的主要内容之一。 世界上有些船厂对批量生产的大型油船的立体分段也采用流水线生产方式进行装焊和船坞总装。 船体总装完成后必须对船体进行密闭性试验,然后在尾部进行轴系和舵系对中,安装轴系、螺旋桨和舵等。 在完成各项水下工程后准备下水。 船舶下水将在船台(坞)总装完毕的船舶从陆地移入水域的过程。 船舶下水时的移行方向或与船长平行,或与船长垂直,分别称为纵向下水和横向下水。 下水滑道主要为木枋滑道和机械化滑道。 前者依靠船舶自重滑行下水,使用较普遍;后者利用小车承载船体在轨道上牵引下水,多用在内河中小型船厂。 纵向下水之前先将搁置在墩木上的船体转移到滑板和滑道上,滑道向船舶入水方向有一定倾斜。 当松开设置于滑板与滑道间的制动装置后,船舶由于自重连同滑板和支架一起滑入水中,然后靠自身的浮力飘浮于水面。 为减少下滑时的摩擦阻力,在滑板与滑道之间常涂上一定厚度的下水油脂;也可用钢珠代替下水油脂,将滑动摩擦改为滚动摩擦,进一步减少摩擦力。 在船坞内总装的船,只要灌水入坞即能浮起,其下水操作比在船台下利用滑道下水简单和安全得多。 下水意味着船舶建造已完成了关键性的、主要的工作。 按传统习惯,大型船舶下水常举行隆重的庆祝仪式。 码头安装(设备和系统的安装)船舶下水后常是靠于厂内舾装码头,以安装船体设备、机电设备、管道和电缆,并进行舱室的木作、绝缘和油漆等工作。 码头安装涉及的工种很多,相互影响也较大。 而随着船舶设备和系统的日趋复杂,安装质量的要求也不断提高,故安装工作直接关系下水后能否迅速试航和交船。 为了缩短下水后的安装周期,应尽可能将上述安装工作提前到分段装配和船体总装阶段进行,称为预舾装。 将传统的单件安装改为单元组装,也可大大缩短安装周期,即根据机舱和其他舱室设备的布置和组成特点确定安装单元的组成程度,如主机冷却单元可包括换热器、泵、温度调节器、带附件的有关管道和单元所必需的电气设备。 在车间内组成安装单元,然后吊至分段、总段或船上安装,这样可使18~25%的安装工作量由船上提前到内场进行,能使船上的安装周期缩短15~20%。 系泊试验和航行试验在船体建造和安装工作结束后,为保证建造的完善性和各种设备工作的可靠性,必须进行全面而严格的试验,通常分为两个阶段,即系泊试验和航行试验。 系泊试验俗称码头试车,是在系泊状态下对船舶的主机、辅机和其他机电设备进行的一系列实效试验,用以检验安装质量和运转情况。 系泊试验以主机试验为核心,检查发电机组和配电设备的工作情况,以便为主机和其他设备的试验创造条件。 对各有关系统的协调、应急、遥测遥控和自动控制等还需要进行可靠性和安全性试验。 系泊试验时船舶基本上处于静止状态,主机、轴系和有关设备系统不能显示全负荷运转的性能,所以还需要进行航行试验。 航行试验是全面地检查船舶在航行状态下主机、辅机以及各种机电设备和系统的使用性能。 通常有轻载试航和重载试航。 在航行试验中测定船舶的航速、主机功率以及操纵性、回转性、航向稳定性、惯性和指定航区的适航性等。 试验结果经验船机构和用户验收合格后,由船厂正式交付订货方使用。 发展近代造船技术的发展过程是由手工操作向机械化、自动化迈进的过程。 自50年代起,船体建造用焊接取代了铆接,使船体建造由过去长期使用的零星散装方式改进为分段装配方式,大大提高了造船效率。 由于船体结构和形状比较复杂,手工操作在船体建造中一直占较大比重。 电子计算机和数控技术的应用正进一步改变造船业的面貌。 电子计算机首先应用于数学放样,进而出现数字输入和图形输出的数控绘图机、数控切割机、数控肋骨冷弯机、数控螺旋桨加工机床和管子加工机床等。 同时电子计算技术还在造船厂的生产管理、计划编制、材料设备供应和成本核算等方面逐渐得到应用。 为减少信息准备工作,消除设计与生产之间的脱节现象,又研制成大型造船集成数控系统,它包括船舶设计、生产和管理等所有功能的通用信息,能协调地完成从设计到生产的整个工作过程。 因此,继续扩大计算机在造船中的应用,是现代发展造船技术、进一步提高造船自动化程度的主要方向。 参考书目王勇毅等著:《船体建造工艺学》,人民交通工业出版社,北京,1980。
电脑开机一会主机断电,显示器有电,再开机,电脑进入断电自检程序,CPU风扇运转
电脑开不了机的几点原因常见故障:一、开机主机显示器不显示,无报警二、开机显示器还是不显示,有报警三、从windows xp那个启动界面进去后就又反复重启四、蓝屏常见故障的分析及解决办法:一、不能开机且无报警的检修思路:造成不能开机且无报警故障的最大可能,也就是最值得怀疑的是:1.供电;;3.主板。 因为这三件硬件只要有一件有故障,主板就不能启动,主板没启动就不会报警。 有故障不一定是配件坏了,接触不良也是故障。 所以按下面的步骤检查:1.测量电源是否能正常输出各路电压,无测量工具时可用好电源直接代换。 电源与主板的连接是否可靠,可拔插20口插头。 面板上的电源开关是否损坏。 必要时可直接短接主板上的PWR SW接针,看能否启动主板。 在确信供电正常后进行下面的检查。 2.拔插CPU,不行的话换CPU。 拔插CPU后能启动,说明是CPU接触不良。 拔插CPU后不能启动,CPU有损坏的可能,所以换CPU,换CPU还是不行,剩下的只有主板了。 3.主板检查首选应是CPU插座供电是否正常,其次是南桥北桥,各晶振,时钟发生器等。 可以借助主板诊断卡。 当然这些不是一般的DIYER能完成的。 只有送修了。 二、常见的PC故碍开机报警声及解决(点击)如果是内存问题:内存没插好,把内存卡拔下来用橡皮擦擦亮金手指,或者内存坏掉其他问题:1.显卡未插紧.2.检查显示器是否损坏.3.将主板上所有连线重新插一次.4.重插PCI,AGP,或其他连接卡.三、可能是系统启动文件损坏或者更换硬件1、显示器的分辨率被调了,在安全模式下卸载了显卡驱动程序,就可以了2、启动文件坏了3、碰到这种情况我的解决办法是,首先,开机按F8,会出来一个界面,那个界面有让你选择进入安全模式等,先选择其中“最后一次正确配置”,如果不行,再选择 “安全模式”,在里面可以重装某硬件驱动程序等,再不行,那就是系统启动文件被破坏了。 4、系统启动文件损坏还有可能是有些人在杀毒的时候把一些东西删了,结果启动不了系统,那么你可以用XP启动盘的修复功能,开机,在BIOS里选择光盘启动,并放入光盘,按R有个XP修复台。 四、蓝屏引起蓝屏的原因很多,有硬件、有软件的,还有其它不易觉察的因素,其解决办法也比较多,下面就你碰到的情况作一下分析,在系统启动和关闭时出现蓝屏一般有以下这些原因:1、硬盘剩余空间太小或碎片太多:必须保证预留有一定的磁盘空间,并在使用电脑隔一段时间后进行一次碎片整理;2、系统硬件冲突:这种现象导致“蓝屏”也比较常见。 实践中经常遇到的是声卡或显示卡的设置冲突。 在“控制面板”→“系统”→“设备管理”中检查是否存在带有黄色问号或感叹号的设备,如存在可试着先将其删除,并重新启动电脑。 若还不行,可手工进行调整或升级相应的驱动程序;3、启动时加载程序过多:不要在启动时加载过多的应用程序,以免使系统资源消耗殆尽;4、应用程序存在着BUG:使用程序存在一些错误或不稳定因素也会引起蓝屏;5、遭到不明的程序或病毒攻击所至:可仔细检查一下,并做好防范措施;6、版本冲突:有些应用程序需调用特定版本的动态链接库DLL,如果在安装软件时,旧版本的DLL覆盖了新版本的DLL,或者删除应用程序时,误删了有用的DLL文件,就可能使上述调用失败,从而出现“蓝屏”。 可重新安装试一试。 7、注册表中存在错误或损坏:很多情况下这是出现“蓝屏”的主要原因。 注册表保存着系统的硬件配置、应用程序设置和用户资料等重要数据,如果注册表出现错误或被损坏,就很可能出现“蓝屏”。 8、软硬件不兼容:新技术、新硬件的发展很快,如果安装了新的硬件常常出现“蓝屏”,那多半与主板的BIOS或驱动程序太旧有关,以致不能很好支持硬件。 如果你的主板支持BIOS升级,应尽快升级到最新版本或安装最新的设备驱动程序。 更多答案解答地址: 希望我的答案能帮助到你
发表评论